E Steps and Flow Rate
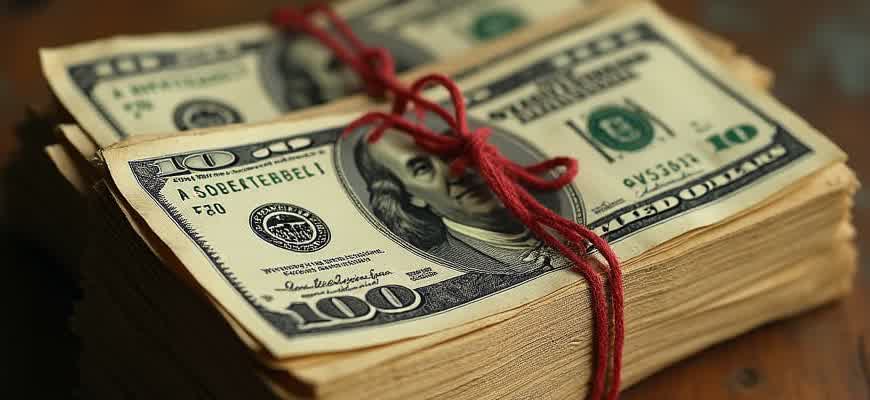
The process of managing the flow rate and E steps is crucial in various industrial applications, especially in fluid dynamics and automation. The flow rate is a measurement of the amount of fluid passing through a system per unit of time, while E steps refer to the number of steps or increments required for a specific process. Together, they influence the precision and efficiency of systems like pumps, motors, and other fluid-handling devices.
To ensure an optimal process, it is necessary to balance the flow rate and E steps. The relationship between these factors often requires the calculation of variables such as speed, pressure, and resistance, which affect the overall performance. Below are the key steps to consider:
- Determine the desired flow rate for the system
- Calculate the number of E steps needed for the operation
- Adjust the system parameters to achieve the target flow rate
- Monitor and fine-tune to ensure accuracy and efficiency
Important: A higher flow rate can lead to increased wear and tear on equipment, so it's vital to consider both speed and pressure limits when adjusting the system.
Here’s a simplified table to illustrate the relationship between flow rate, pressure, and the required E steps:
Flow Rate (L/min) | Pressure (Bar) | E Steps |
---|---|---|
10 | 3 | 500 |
20 | 5 | 800 |
30 | 7 | 1200 |
How E-Step Calibration Affects Flow Rate Performance Across Various Sectors
The accuracy of e-steps calibration directly influences the flow rate in various manufacturing and production processes. In industries that rely on precise fluid or material dispensation, such as pharmaceuticals, food production, or 3D printing, even small errors in e-step configuration can lead to significant inefficiencies. Proper calibration ensures consistent output, prevents waste, and maintains quality standards. Understanding how e-steps impact the flow rate can optimize performance and reduce operational costs.
Each sector has unique requirements for flow rate control, and as such, the impact of e-steps can vary. In some industries, even slight variations in flow rate can lead to production delays, while in others, it could affect the end product's quality. Below, we discuss how e-steps play a crucial role in maintaining the desired flow rate in different industries.
Pharmaceutical Industry
In pharmaceutical production, the accuracy of dispensing liquids or powders is critical. The flow rate must be tightly controlled to ensure that the correct dosage is administered. Inaccurate e-step calibration can lead to deviations in the amount of active ingredients, potentially affecting the efficacy of the product.
- Critical Factors: Precision in dispensing, regulatory compliance, product consistency.
- Impact of Incorrect E-Steps: Variability in active ingredient concentrations, potential product recalls, legal penalties.
Even small e-step discrepancies can result in significant variations in the final product, leading to potential risks to public health and costly regulatory violations.
Food and Beverage Manufacturing
In the food industry, where ingredient flow rates affect taste, texture, and overall product quality, e-step calibration is equally important. For example, in processes like beverage mixing or dough preparation, errors in the flow rate can alter the product’s taste and consistency.
- Key Elements: Ingredient balance, uniformity, production speed.
- Consequences of Errors: Product inconsistency, consumer dissatisfaction, waste generation.
3D Printing
In additive manufacturing, e-step calibration affects the extrusion of filament or resin. Incorrect settings can cause either under-extrusion or over-extrusion, leading to weak prints, excess material use, and defects.
Issue | Impact |
---|---|
Under-Extrusion | Weak prints, poor layer adhesion, printing failures. |
Over-Extrusion | Excess material usage, increased print time, rough surface finish. |
Key Factors Affecting Flow Rate and How E Steps Can Optimize Them
Flow rate is a critical parameter in numerous industrial and engineering applications, determining the efficiency and productivity of systems like pumps, turbines, and valves. Several factors influence how efficiently a fluid flows through a system, including pressure, temperature, viscosity, and pipe dimensions. Understanding these factors is essential to optimizing flow rates and minimizing energy losses.
The "E Steps" approach provides a structured method to adjust operational settings, optimizing flow by systematically analyzing and adjusting these influencing factors. By fine-tuning these parameters, engineers can ensure more consistent, efficient, and reliable flow across systems, reducing the likelihood of performance degradation.
Factors Impacting Flow Rate
- Pressure Difference: A greater pressure difference between the inlet and outlet increases flow rate, provided the system is not constrained by pipe diameter or other restrictions.
- Fluid Viscosity: Higher viscosity fluids resist flow, reducing the flow rate. E Steps can help reduce viscosity via temperature control or by using additives that enhance fluid flow.
- Pipe Dimensions: The diameter and length of pipes directly affect the flow rate. Larger diameter pipes reduce resistance, leading to higher flow rates.
- System Resistance: Valves, bends, and fittings add resistance, slowing the flow. Optimizing the placement and types of components can minimize losses.
Optimizing Flow with E Steps
- Adjusting Pressure Settings: By fine-tuning pressure conditions, E Steps can minimize energy usage and optimize flow through the system without excessive stress on components.
- Controlling Fluid Properties: The implementation of E Steps helps maintain consistent fluid properties, like temperature, which can reduce viscosity and increase flow rate.
- Upgrading Infrastructure: Replacing or resizing pipes and valves can be guided by E Steps to ensure that system resistance is minimized, directly improving flow rates.
"Optimizing flow rates through careful control of pressure, viscosity, and pipe design leads to a more efficient system, reducing both operational costs and the likelihood of maintenance issues."
Example: Flow Optimization Table
Factor | Impact on Flow Rate | E Step Action |
---|---|---|
Pressure | Higher pressure leads to faster flow | Adjust inlet/outlet pressure for optimal balance |
Viscosity | Higher viscosity decreases flow | Control temperature or use additives |
Pipe Diameter | Wider pipes allow higher flow rates | Increase diameter or replace pipes if necessary |
System Resistance | Increased resistance slows flow | Optimize component placement and design |
Addressing Common Challenges in Implementing E Steps for Flow Rate Control
Configuring the correct E steps is critical for accurate flow rate control in 3D printing. However, achieving precise control can be challenging due to several factors that affect the accuracy of the extruder's steps per millimeter. One of the main difficulties lies in the calibration process itself, as incorrect values can lead to over-extrusion or under-extrusion, resulting in poor print quality. The flow rate control requires continuous fine-tuning, especially when using different materials or printer configurations.
Another issue that arises is the variation in filament diameter, which can significantly affect the extrusion volume. Even slight differences in filament thickness can lead to inconsistent extrusion, making it harder to maintain precise flow rates. It is crucial to account for these variations by measuring the filament's diameter at multiple points before calibration and regularly throughout the printing process.
Common Challenges in E Steps Calibration
- Inaccurate Calibration: Incorrect E step values can result in over-extrusion or under-extrusion.
- Filament Diameter Variations: Fluctuations in filament thickness can cause inconsistent extrusion rates.
- Temperature Fluctuations: Temperature changes can alter the viscosity of the material, affecting the flow rate.
- Wear and Tear: Extruder gears and hotend components may wear out over time, affecting extrusion accuracy.
Steps to Address These Issues
- Measure Filament Diameter: Regularly measure the filament diameter at multiple points to account for any inconsistencies.
- Calibrate E Steps Regularly: Perform periodic calibration to ensure the steps per millimeter remain accurate over time.
- Monitor Temperature: Maintain a stable temperature to prevent variations in material flow.
- Replace Worn Components: Ensure extruder parts, such as gears, are replaced when signs of wear appear.
Note: Regular maintenance and recalibration are key to ensuring the longevity and accuracy of the flow rate control system in 3D printers.
Impact of Incorrect E Steps on Print Quality
Problem | Effect | Solution |
---|---|---|
Under-extrusion | Inadequate material flow, causing gaps and weak layers. | Increase E steps and ensure filament diameter consistency. |
Over-extrusion | Excess material causing blobs and stringing. | Reduce E steps and calibrate frequently. |