Autopilot Troubleshooting
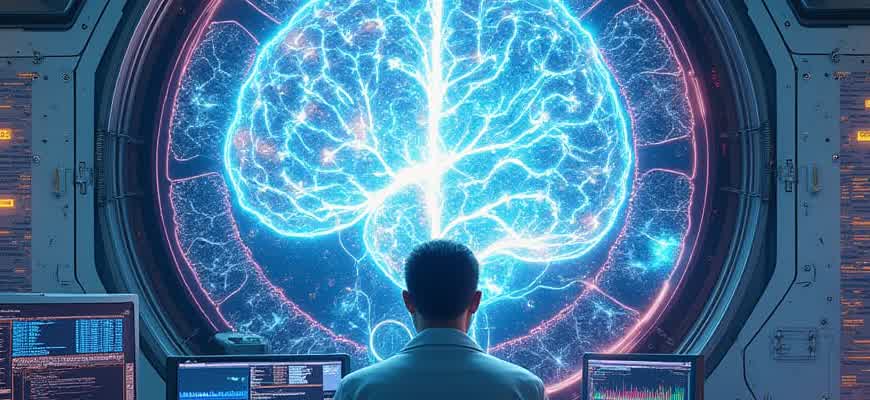
When troubleshooting autopilot issues, it's essential to systematically approach the problem, focusing on the main components and their interactions. Begin by identifying whether the malfunction is due to hardware or software. This will help narrow down the potential causes.
Steps to Begin Troubleshooting:
- Check the power supply to the autopilot system.
- Inspect for any recent software updates or changes.
- Verify that the sensors are calibrated properly.
- Examine the autopilot mode settings for any configuration errors.
Common Hardware Issues:
- Faulty sensors or wiring connections.
- Power interruptions or failures in critical components.
- Defective actuator systems causing incorrect steering behavior.
Important: Always reset the system after addressing any hardware failures to ensure correct functionality.
Diagnostic Table:
Issue | Potential Cause | Solution |
---|---|---|
System Not Responding | Power supply failure | Check fuses and connections. |
Erratic Behavior | Sensor miscalibration | Recalibrate sensors. |
Mode Switching Problems | Software glitch | Update or reinstall the software. |
Diagnosing Common Autopilot System Failures
Autopilot systems are complex and critical components in modern aviation, and their failure can lead to serious consequences if not properly diagnosed. Understanding the common issues that can occur within these systems and knowing how to troubleshoot them is crucial for ensuring safety and functionality. Below are some of the most frequent failures and their potential causes.
Autopilot system failures can manifest in various ways, including unresponsive controls, erroneous flight path adjustments, and sudden disengagements. The troubleshooting process involves a systematic approach, from basic electrical checks to in-depth software diagnostics. The table below outlines some of the most common failures and their associated troubleshooting steps.
Failure | Possible Cause | Troubleshooting Steps |
---|---|---|
Unresponsive Autopilot | Electrical power loss, faulty wiring |
|
Erratic Flight Path Adjustments | Sensor calibration error, software glitch |
|
Autopilot Disengagement | Control inputs, system overload |
|
Note: Regular maintenance and system checks are essential in preventing autopilot system failures. It is recommended to follow manufacturer guidelines for troubleshooting and routine inspections.
In addition to these common failures, pilots should always refer to the aircraft's manual and use specialized diagnostic tools to ensure accurate troubleshooting. Identifying the root cause quickly and efficiently can prevent unnecessary downtime and ensure smooth operations.
Step-by-Step Guide to Troubleshooting Sensor Malfunctions
When diagnosing issues with autopilot sensors, a structured approach is crucial for identifying and resolving malfunctions effectively. Sensors play a key role in the autopilot system, providing essential data for navigation, speed, and altitude. A malfunction can result in erratic behavior or complete system failure, requiring immediate attention.
Start by verifying the integrity of the sensor hardware before diving into software or configuration issues. Follow these systematic steps to ensure a thorough troubleshooting process:
1. Initial Checks
- Ensure that the sensor is powered on and connected to the system.
- Inspect cables and connectors for any visible signs of wear or damage.
- Check the sensor’s physical condition, such as signs of dirt or corrosion.
2. Verify Sensor Calibration
- Check if the sensor has been calibrated recently. Calibration may drift over time.
- Perform a manual calibration if the sensor’s readings seem off.
- Ensure that the environment where the sensor operates is within the specified range (e.g., temperature, humidity).
3. Software Diagnostics
- Run a diagnostic test to check if the system detects the sensor correctly.
- Ensure that software updates are applied, as outdated software may cause compatibility issues.
- Check the sensor’s readings in the software interface and compare them with expected values.
4. Examine Data Feed and Signal Processing
If the sensor is receiving power and calibrated correctly, but readings still seem inaccurate, the issue might lie with signal processing. Perform the following steps:
- Verify that the sensor's data is being transmitted properly to the autopilot system.
- Check for interference or signal loss, especially in environments with high electromagnetic activity.
5. Test with Backup Sensors
If available, replace the malfunctioning sensor with a backup or substitute it with a different sensor of the same type. If the problem resolves, the original sensor may need replacement.
6. Final Verification
After resolving the issue, perform a series of tests to ensure that the system is functioning properly. Make sure the autopilot responds correctly to changes in sensor data.
Note: Always follow manufacturer guidelines and perform tests in a controlled environment to avoid further complications during troubleshooting.
Common Sensor Malfunctions and Symptoms
Malfunction | Symptoms |
---|---|
Calibration Drift | Erratic or inconsistent sensor readings. |
Connection Failure | No data transmission or error messages in the system. |
Signal Interference | Unusual sensor behavior, such as fluctuating data or total failure. |
Resolving Communication Issues Between Autopilot and Aircraft Systems
Effective communication between the autopilot system and aircraft components is essential for safe and efficient operation. Disruptions in this communication can lead to operational failures and compromise flight safety. Understanding the underlying causes of communication issues is crucial for resolving them promptly.
Several factors can cause communication breakdowns between the autopilot and aircraft systems, including hardware malfunctions, software bugs, or faulty connections. Identifying these issues requires a methodical approach and troubleshooting process to restore proper functioning.
Common Causes of Communication Failures
- Faulty Wiring or Connections: Loose or damaged cables can interrupt signals between systems.
- Software Glitches: Incompatibilities or errors in the autopilot's software can result in communication failures.
- Sensor Malfunctions: Inaccurate data from sensors such as the attitude indicator can mislead the autopilot system.
- Power Supply Issues: Insufficient power to key components may cause the autopilot to lose connection with other systems.
Troubleshooting Steps
- Check Wiring and Connections: Inspect all wiring and connectors for signs of wear, corrosion, or disconnections.
- Verify Software Integrity: Ensure that all software updates have been properly installed and there are no compatibility issues.
- Test Sensors: Perform sensor calibration checks to ensure the autopilot is receiving accurate data.
- Inspect Power Supply: Confirm that the electrical system is providing adequate power to the autopilot and associated components.
Key Considerations
Always perform regular maintenance and checkups to prevent potential communication issues. Early detection can prevent serious problems during flight.
Diagnostic Tools
Tool | Description |
---|---|
Flight Data Recorder | Tracks autopilot performance and provides valuable data for identifying issues. |
Autopilot Diagnostic Software | Allows for real-time monitoring and troubleshooting of autopilot systems. |
Electrical Testing Equipment | Used to test the integrity of power supply systems and identify power-related issues. |
Solving Power Supply Issues Affecting Autopilot Functionality
Power supply irregularities can be a major cause of malfunction in autopilot systems, leading to inconsistent performance or complete system failure. These issues can range from power surges to inadequate voltage levels, and they can manifest in various ways depending on the specific autopilot hardware and software configurations. A well-maintained and stable power supply is crucial for ensuring reliable operation of critical flight instruments and control systems.
Understanding the root causes of power-related problems and their impact on autopilot systems is key to troubleshooting effectively. Below are some common sources of power supply issues, along with methods to address them:
Common Causes and Solutions
- Voltage Fluctuations: Variations in voltage can lead to erratic autopilot behavior, including loss of control or system resets. Ensure voltage regulators are functioning properly and inspect power lines for potential disruptions.
- Battery Depletion: A weak or damaged battery may not provide sufficient power to the autopilot system, leading to incomplete or malfunctioning operations. Regularly monitor battery levels and replace them as necessary.
- Faulty Wiring Connections: Loose or corroded connections can result in intermittent power loss. Perform regular checks on all wiring and connections, especially those leading to key system components.
Steps for Troubleshooting Power Supply Issues
- Step 1: Check the voltage readings at various points in the power circuit to identify any discrepancies from the expected range.
- Step 2: Inspect the power supply for any signs of overloading or overheating that may indicate an underlying issue.
- Step 3: Test the integrity of the battery and replace it if its capacity is below the required threshold for autopilot operation.
- Step 4: Examine wiring and connectors for damage, corrosion, or loose connections. Ensure all cables are securely fastened.
Proper power management is essential for ensuring the safe and efficient operation of autopilot systems. Regular maintenance and monitoring can help avoid costly repairs and prevent system failures in critical situations.
Power Supply Test Table
Component | Possible Issue | Solution |
---|---|---|
Voltage Regulator | Voltage instability or irregularities | Replace or recalibrate the regulator |
Battery | Insufficient charge or capacity | Replace the battery and ensure correct charging procedures |
Wiring | Loose or damaged connections | Repair or replace wiring and connectors |
Understanding and Fixing Autopilot Software Bugs
Autopilot systems rely on highly complex software to function correctly. However, bugs can occur due to errors in code, improper system configurations, or external factors like sensor malfunctions. Troubleshooting these issues often requires a methodical approach to pinpoint the exact cause and apply the necessary fixes. Understanding the software components and the interactions between different system parts is crucial for diagnosing and resolving these problems.
When dealing with autopilot software bugs, it's essential to follow a structured process. Identifying the root cause of a malfunction can be time-consuming, but employing systematic debugging practices can significantly reduce troubleshooting time. Common issues include faulty algorithm calculations, data inconsistencies, or communication failures between the autopilot and external systems.
Steps to Resolve Autopilot Software Bugs
- Check System Logs: Begin by analyzing system logs and error reports to identify any irregularities or error messages.
- Validate Sensor Data: Ensure that all sensors providing input to the autopilot are functioning correctly. Sensor failures or miscalibrations can cause incorrect data to be sent to the software.
- Test Algorithm Logic: Verify the autopilot’s control algorithms to ensure they are processing data correctly and making decisions based on accurate inputs.
- Run Software in Simulated Environment: Simulate the autopilot’s operations in a controlled environment to isolate and reproduce the bug.
- Update Software: Make sure the latest software patches and updates are installed, as bugs may have already been addressed in newer versions.
Key Considerations
Always prioritize safety and avoid making changes to the system while in operation. Perform troubleshooting steps in a controlled environment or during scheduled maintenance windows to minimize risks.
Common Software Bugs in Autopilot Systems
Bug Type | Description | Fix |
---|---|---|
Control Algorithm Failure | Incorrect processing of input data leading to unexpected behavior. | Debug and optimize algorithm logic. |
Sensor Data Discrepancy | Inaccurate sensor readings affecting navigation decisions. | Calibrate sensors or replace faulty hardware. |
Software Version Incompatibility | Older software versions causing conflicts with newer components. | Update the software to the latest version. |
Final Thoughts
Understanding the complexities of autopilot software and having a clear strategy for troubleshooting can significantly reduce downtime and ensure the reliability of the system. Regular maintenance and updates are key to preventing issues before they become critical problems.
Optimizing Autopilot Performance Through Calibration Adjustments
Proper calibration of the autopilot system is critical for ensuring its accuracy and efficiency during flight. Without correct calibration, the system may experience errors in navigation, control, and response times. Fine-tuning the calibration settings helps to maintain the optimal functionality of various components, from sensors to control surfaces, ensuring smoother operations and enhanced safety.
Adjusting calibration settings is typically done through the flight management system (FMS) or a dedicated autopilot configuration tool. These settings include a variety of parameters, such as sensor offsets, gain values, and trim adjustments, which need to be customized based on the aircraft's specific flight characteristics and mission requirements.
Calibration Steps for Autopilot Systems
- Sensor Calibration: This involves aligning and adjusting the aircraft’s attitude, heading, and altitude sensors. Ensuring that the sensors are correctly aligned prevents errors in flight path tracking.
- Control Surface Adjustments: Calibration of control surfaces (e.g., ailerons, elevators) ensures that autopilot commands are accurately executed, maintaining smooth and stable flight.
- Gain and Trim Settings: Adjusting the gain and trim ensures that the autopilot system responds optimally to flight conditions, such as turbulence or changes in load.
Steps to Adjust Calibration Settings
- Connect to the aircraft’s autopilot system interface.
- Access the calibration settings menu.
- Check sensor alignment and correct any misalignments detected.
- Adjust control surface trim and gain values based on test flights and environmental conditions.
- Conduct a flight test to validate changes and ensure performance is up to standards.
Important: Always refer to the manufacturer’s manual when adjusting calibration settings to ensure the aircraft's autopilot system remains within safe operational limits.
Calibration Checklist
Step | Action | Notes |
---|---|---|
1 | Sensor alignment | Check if sensors report correct data values. |
2 | Control surface trim | Ensure that surfaces are aligned and responsive to autopilot commands. |
3 | Gain adjustments | Fine-tune for optimal autopilot response under different conditions. |
When to Seek Professional Help: Autopilot System Repair vs. Troubleshooting
Maintaining the functionality of an autopilot system is crucial for ensuring the safety and efficiency of your vessel. Troubleshooting minor issues can be done by most experienced users, but some situations require the expertise of a professional technician. Understanding the difference between repair and troubleshooting is vital in making the right decision about when to call for help.
While troubleshooting involves identifying and resolving simple issues like software glitches or sensor misalignment, repairs typically require specialized tools, knowledge, and access to replacement parts. Knowing when to call a professional can save time, prevent further damage, and avoid unnecessary costs.
When Troubleshooting is Sufficient
- Minor software issues: If the autopilot’s interface is not responding or displays error messages, restarting the system or updating the software might resolve the issue.
- Sensor recalibration: When the system’s sensors are misaligned, recalibrating them according to the manufacturer’s instructions can often restore functionality.
- Electrical connections: Loose or disconnected wires can sometimes be fixed by tightening or reconnecting them, provided they are easily accessible.
When a Professional is Needed
- Severe hardware failure: If you suspect internal damage to the autopilot’s mechanical components, such as the drive motor or control unit, professional repair is required.
- Complex system malfunctions: Issues involving multiple interconnected subsystems (e.g., navigation, power supply, or communications) usually require a technician with the necessary diagnostic tools.
- Software corruption: In cases where the system cannot be reset or reprogrammed by the user, a professional may need to reinstall or reconfigure the software.
Comparison Table
Issue Type | Solution | Professional Required? |
---|---|---|
Minor glitches | Restarting system, updating software | No |
Sensor misalignment | Recalibration | No |
Hardware failure | Part replacement or repair | Yes |
System-wide malfunction | Full diagnostic and repair | Yes |
It's important to assess the complexity of the issue before deciding whether to proceed with troubleshooting or seek professional help.
Preventative Measures to Avoid Future Autopilot System Issues
Maintaining an autopilot system in peak condition requires proactive measures to prevent potential issues. Regular checks and updates are key in ensuring that the system operates smoothly and without interruptions. A combination of routine maintenance and awareness of environmental factors can significantly reduce the likelihood of encountering problems with the autopilot functionality. It's crucial to address both software and hardware components to avoid system failures during critical moments.
Establishing clear procedures for troubleshooting and performing regular system assessments is essential. This includes monitoring the autopilot's interaction with sensors, ensuring proper calibration, and updating software to adapt to any new system improvements. By following a structured approach to system care, operators can enhance reliability and reduce system downtimes.
Recommended Preventative Measures
- Conduct routine diagnostics on sensors and hardware components
- Regularly update software to ensure compatibility with the latest features
- Monitor environmental factors such as weather conditions that could affect system performance
- Train personnel to identify early signs of system malfunction
- Verify proper integration of autopilot with other onboard systems
Maintenance Checklist
Task | Frequency | Responsible Party |
---|---|---|
Hardware diagnostics | Monthly | Maintenance Team |
Software update installation | Every 3 months | Technical Team |
System calibration | Quarterly | Operators |
Important: Consistent software updates and regular calibration checks are essential to prevent unexpected errors that may arise from outdated system components.