7 Quality Tools Six Sigma
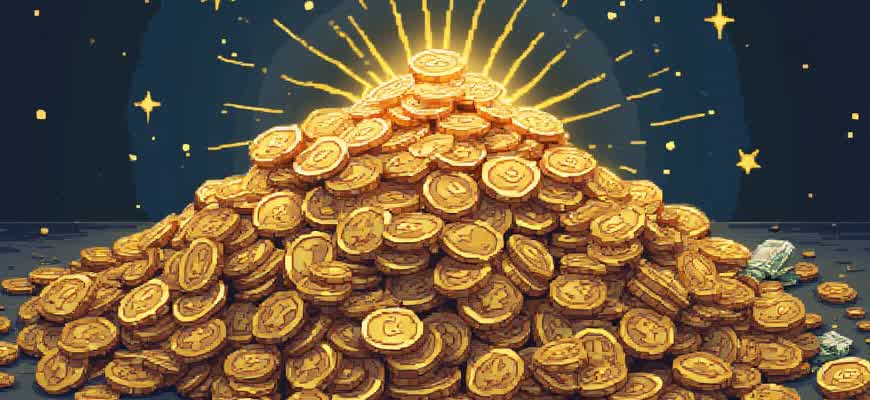
Six Sigma methodology utilizes several core tools to improve quality and optimize processes. These tools help to identify inefficiencies, reduce variations, and enhance overall performance in any organizational process. Below is an overview of the most important quality tools used in Six Sigma:
- Flowchart - Visual representation of a process that outlines the sequence of steps, making it easier to identify bottlenecks and inefficiencies.
- Cause-and-Effect Diagram - Also known as a Fishbone diagram, it is used to identify the root causes of problems in a process.
- Check Sheet - A structured form used to collect data systematically, often used for counting occurrences of specific events.
- Histogram - A graphical representation of data distribution, helpful for understanding variations within a process.
- Control Chart - A tool that monitors process stability and identifies trends over time, enabling early detection of deviations.
- Pareto Chart - A bar chart that shows the frequency of problems or causes in descending order, illustrating the most significant issues.
- Scatter Diagram - A plot used to identify relationships between two variables, often used in identifying correlations between cause and effect.
The use of these tools is fundamental for maintaining process quality. Below is a brief summary of each tool's application:
Tool | Purpose |
---|---|
Flowchart | Maps process steps to identify inefficiencies. |
Cause-and-Effect Diagram | Identifies potential causes of problems in a process. |
Check Sheet | Collects data systematically for analysis. |
Histogram | Visualizes data distribution and variations. |
Control Chart | Monitors process performance over time. |
Pareto Chart | Helps prioritize problems by their impact. |
Scatter Diagram | Analyzes correlations between variables. |
These tools are essential in ensuring the continuous improvement of processes and in achieving higher efficiency and quality standards.
How to Implement the Pareto Chart in Your Six Sigma Projects
In Six Sigma projects, the Pareto Chart is a powerful tool that helps identify the most significant issues affecting the process. It is particularly useful for prioritizing problems, allowing teams to focus their efforts on the areas with the highest impact. By utilizing the Pareto principle (80/20 rule), the chart highlights the vital few factors that cause the majority of problems, guiding teams toward effective solutions.
Implementing the Pareto Chart begins with gathering data on the issues or defects present in the process. Once the data is collected, it can be analyzed and displayed on the chart to visually emphasize the most common problems. Below is a step-by-step approach to using the Pareto Chart in Six Sigma projects:
- Data Collection: Gather data on defects, errors, or issues that occur in your process. This can include customer complaints, machine failures, or quality control defects.
- Frequency Analysis: Count how often each problem occurs. Group similar issues together to simplify the analysis.
- Calculate Cumulative Percentages: Rank the issues from most frequent to least frequent, and calculate their cumulative percentage to identify which ones are most critical.
- Create the Chart: Use a bar chart to plot the frequency of each issue. The bars should be arranged in descending order, and a cumulative line should be added to show the cumulative percentage.
- Interpret Results: Focus on the largest bars (the most frequent problems) and use the cumulative line to determine which issues contribute the most to the overall process variation.
"By focusing on the 20% of causes that create 80% of the problems, teams can significantly improve the process by addressing the most impactful issues first."
Here's an example of a Pareto Chart for a manufacturing defect analysis:
Defect Type | Frequency | Cumulative Percentage |
---|---|---|
Defective Product | 150 | 30% |
Packaging Errors | 120 | 55% |
Assembly Mistakes | 90 | 75% |
Material Defects | 60 | 85% |
Other | 50 | 100% |
Key Benefits of Using a Cause-and-Effect Diagram for Root Cause Analysis
One of the most effective tools for identifying the underlying factors behind a problem is the Cause-and-Effect diagram, also known as the Fishbone diagram. It is widely used in Six Sigma methodologies to visually break down potential causes of an issue into more manageable categories. This method enables teams to explore all possibilities systematically, making it easier to spot the root causes of a problem.
By using this diagram, organizations can clearly map out the relationships between various factors and the effect they have on a specific outcome. This organized approach ensures that the analysis is thorough and helps prioritize areas for improvement based on their potential impact on the problem at hand.
Advantages of Cause-and-Effect Diagram in Root Cause Analysis
- Structured Approach: The diagram provides a clear visual framework for analyzing complex problems, helping teams avoid overlooking important details.
- Identifies Systemic Issues: It allows teams to uncover root causes within processes, systems, or human factors that may be contributing to the issue.
- Engages the Entire Team: The collaborative nature of creating a Cause-and-Effect diagram encourages team participation, leading to more comprehensive insights.
How the Diagram Facilitates Analysis
- Clarifies Problem Areas: The diagram breaks down the problem into categories such as methods, materials, equipment, and people, making it easier to pinpoint where the issue lies.
- Identifies Interdependencies: By visualizing the various factors, teams can see how different elements are interconnected, which helps in understanding the bigger picture.
- Prioritizes Actions: Once the root causes are identified, the team can focus on the most impactful solutions first, streamlining the improvement process.
The Cause-and-Effect diagram is invaluable in helping teams stay focused on the problem’s root causes, rather than its symptoms. This focus leads to more sustainable, long-term improvements in the process.
Benefit | Explanation |
---|---|
Visual Clarity | Helps clarify complex problems by breaking them down into easily digestible components. |
Enhanced Collaboration | Encourages team collaboration, which leads to a broader perspective and more accurate conclusions. |
Effective Root Cause Identification | Allows for a thorough investigation into all possible causes, ensuring that no potential factor is overlooked. |
Steps to Create a Control Chart for Ongoing Process Monitoring
Creating a control chart is essential for monitoring ongoing processes to ensure consistency and detect any variations. This tool is particularly useful in identifying when a process is deviating from its standard performance, helping teams take corrective action before issues escalate. A control chart visually represents data over time, showing process behavior and trends that may signal the need for intervention.
The process of developing a control chart requires careful planning and attention to detail. It involves defining critical process parameters, collecting relevant data, and analyzing the results to create an effective monitoring system. Below are the key steps involved in constructing a control chart.
Steps for Creating a Control Chart
- Define the Process and Data Collection Criteria: Identify the key process you wish to monitor and determine which variables or attributes are critical to track.
- Gather Data: Collect data at regular intervals under normal operating conditions. This will serve as your baseline to detect any variations.
- Calculate Control Limits: Compute the upper and lower control limits (UCL and LCL) based on the collected data. These limits indicate the acceptable variation in the process.
- Plot the Data: Create a time-ordered plot of the collected data and place the calculated control limits on the same graph to visualize process stability.
- Interpret the Results: Analyze the chart for any data points that fall outside the control limits or exhibit non-random patterns. These may indicate a need for process adjustment.
It is crucial to consistently update the control chart as new data is collected. Regular monitoring will help detect issues early and ensure the process remains within desired parameters.
Example Control Chart Data
Sample | Value | UCL | LCL |
---|---|---|---|
1 | 45 | 50 | 40 |
2 | 47 | 50 | 40 |
3 | 52 | 50 | 40 |
4 | 49 | 50 | 40 |
5 | 46 | 50 | 40 |
Mastering Flowcharts: A Tool for Streamlining Your Six Sigma Process
Flowcharts are a powerful visual tool in Six Sigma methodology, offering a clear and structured approach to process mapping. By visually representing the steps in a process, flowcharts help identify inefficiencies and potential areas for improvement. They simplify complex workflows, making them more accessible for analysis and optimization. Flowcharts provide a quick overview, enabling teams to pinpoint bottlenecks and non-value-adding activities.
Integrating flowcharts into the Six Sigma process ensures better communication among team members, allowing for a shared understanding of the process and its key components. They are essential when documenting and analyzing processes, making them easier to evaluate and optimize over time. Mastering this tool can significantly contribute to achieving the desired process improvements and driving operational excellence.
Key Elements of Flowcharts
- Start/End Points: Indicate the beginning and conclusion of the process.
- Process Steps: Represent individual actions or tasks that are part of the workflow.
- Decision Points: Identify where decisions must be made that affect the direction of the process.
- Arrows: Show the flow and sequence of activities.
When to Use Flowcharts
- When mapping out a new process for the first time.
- During process improvements to understand current workflows and identify inefficiencies.
- For training and onboarding purposes, making it easier to communicate processes to new team members.
Tip: Flowcharts are most effective when they are simple and easy to follow. Avoid overcrowding them with too many details–focus on key steps and decision points.
Flowchart Example: Process Evaluation
Step | Action | Outcome |
---|---|---|
1 | Identify process | Understand the scope of the process. |
2 | Map process steps | Visualize the flow of actions. |
3 | Analyze decision points | Identify opportunities for improvement. |
Using a Histogram for Data Distribution Analysis in Six Sigma
A histogram is a vital tool for visualizing the distribution of data in Six Sigma projects. It provides an effective way to assess the frequency of data points across different intervals, allowing teams to identify patterns, variations, and potential areas for improvement. By displaying data in a bar graph format, a histogram makes it easier to spot trends, central tendencies, and outliers within the process. This tool helps teams evaluate whether their processes are stable and capable of meeting customer requirements, which is central to Six Sigma methodology.
To use a histogram for data analysis in Six Sigma, first gather a sufficient sample of process data. Then, define the appropriate range of data intervals (bins) that will help in revealing the distribution clearly. Each bar in the histogram represents the frequency of data points within a particular interval. A well-constructed histogram can reveal whether the data follows a normal distribution, has skewness, or exhibits other irregularities that may indicate process issues.
Steps to Construct and Use a Histogram
- Collect Data: Gather process data over a specified period, ensuring the sample size is large enough for meaningful analysis.
- Define Bins: Divide the range of data values into intervals (bins) that will categorize the data.
- Count Data Points: For each bin, count how many data points fall within its range.
- Create Histogram: Plot the bins on the x-axis and the corresponding frequencies on the y-axis. Each bar height represents the frequency of data in that interval.
- Analyze the Results: Look for patterns such as normal distribution, skewed data, or gaps. These patterns provide insight into process stability.
Example of a Histogram Analysis
Bin Range | Frequency |
---|---|
0-10 | 5 |
10-20 | 8 |
20-30 | 12 |
30-40 | 6 |
40-50 | 4 |
Histograms are not just for identifying data distributions but also for detecting anomalies in the process. For example, a bimodal distribution could suggest that two distinct processes or issues are affecting the performance, requiring further investigation.
Practical Tips for Deploying Scatter Diagrams in Process Improvement
Scatter diagrams are an invaluable tool in Six Sigma for identifying relationships between variables and understanding process behavior. By visualizing data points on a two-dimensional graph, they allow teams to spot trends, correlations, and potential issues. However, to effectively deploy scatter diagrams, it's essential to follow a few practical guidelines to ensure they provide meaningful insights.
Before creating a scatter diagram, ensure the data being used is accurate and relevant. Selecting the right variables is crucial, as the diagram's effectiveness depends on the quality of the data. Additionally, be mindful of the scale and measurement units to avoid misinterpretation. Here are some practical tips for deploying scatter diagrams:
- Define Clear Objectives: Before plotting any data, determine the specific process improvement goal. Ask yourself whether the diagram is meant to identify trends, understand variability, or isolate root causes.
- Use Sufficient Data: A small sample size may lead to misleading conclusions. Ensure you have enough data to establish a meaningful correlation, preferably from multiple cycles or time periods.
- Label Axes Properly: Always label both axes clearly with appropriate units of measurement. This helps in accurately interpreting the data and identifying patterns more easily.
- Look for Outliers: Scatter diagrams can reveal outliers that could indicate unusual process behavior. Investigating these points can provide valuable insights into specific anomalies or errors.
“Scatter diagrams are powerful when used with clear objectives and quality data, providing actionable insights into process behavior and improvement opportunities.”
Key Tips for Effective Scatter Diagrams
- Consider the Data Distribution: Determine if the data follows a linear or non-linear pattern. This will help in selecting appropriate analysis methods for process improvements.
- Perform Regression Analysis: To understand the relationship between variables, consider performing a regression analysis in conjunction with the scatter diagram.
- Use Multiple Plots: If you're analyzing multiple variables, use separate scatter diagrams for clarity and better insight. This allows a more granular analysis.
By following these steps, teams can effectively deploy scatter diagrams as part of a larger Six Sigma strategy, leading to more accurate data interpretation and improved process performance.
Tip | Why It Matters |
---|---|
Define Clear Objectives | Ensures the diagram serves a purpose and is aligned with the process improvement goal. |
Use Sufficient Data | Helps establish a reliable correlation and reduces the risk of misleading conclusions. |
Look for Outliers | Outliers can reveal important insights into unexpected process behaviors or errors. |
Why and How to Incorporate a Check Sheet in Six Sigma Data Collection
Incorporating a check sheet in Six Sigma data collection is essential for ensuring that data is gathered in a structured and organized manner. A check sheet provides a straightforward approach to record observations, categorize them, and identify patterns. By using this tool, teams can focus on critical data points without the risk of missing valuable information. It serves as a baseline for analyzing defects, errors, or patterns within the process, which is vital for problem-solving and continuous improvement.
Check sheets simplify the data collection process, offering clarity and accuracy in real-time analysis. They are especially useful when frequent, repetitive observations are required. The simplicity and ease of use of check sheets make them a preferred choice when gathering data in situations that require high efficiency and minimal complexity. By incorporating them into the Six Sigma methodology, teams can enhance their data-driven decision-making and improve process performance.
Benefits of Using a Check Sheet
- Improves Data Accuracy: By standardizing the format for data collection, check sheets help eliminate errors and inconsistencies.
- Easy to Use: Check sheets are simple, requiring little training or expertise to be used effectively by team members.
- Efficient Data Collection: Allows for quick and systematic recording of data, enabling real-time analysis and decisions.
How to Use a Check Sheet in Six Sigma
- Define the Purpose: Clearly state what data needs to be collected and what the goals are for this data.
- Design the Sheet: Structure the check sheet to capture all necessary information, such as the frequency of events, types of defects, or specific time intervals.
- Collect Data: During the process, record observations on the check sheet regularly and consistently to ensure accuracy.
- Analyze Results: After data collection, review the patterns and trends identified in the check sheet, and use this information for process improvement.
"A well-organized check sheet ensures that data collection is both structured and aligned with the objectives of Six Sigma, helping teams to pinpoint areas that need improvement."
Example of a Check Sheet
Defect Type | Frequency | Time of Occurrence |
---|---|---|
Scratches | 15 | 10:00 AM |
Missing Components | 8 | 2:30 PM |
Color Mismatch | 4 | 12:15 PM |